제 2차 세계대전 이후, 산업계는 두 가지 요인으로 성장하였다. 그 첫 번째는 제 2차 세계 대전 이후, 다수의 제품으로 실현된 기술 혁신이다. 다른 하나는 소비자의 구매 욕구를 충족시킬 수 있는 가격으로 제품 공급이 가능하게 된 대량 생산 체계다. 그러므로 1960년대부터 1980년대까지, 생산 능력을 제공하는 설계와 개발 부문이 조직의 핵심 영역이었다. 수요 증가에 대응하기 위한 생산량 증대 노력은 기존 프로세스의 개선이 아니라 신규 증설에 집중되었다. 경영진의 관심 또한 마찬가지였다.
한편, 생산 시스템이 생산 목표를 달성하고 성능을 유지할 수 있을 때, 모든 이해 관계자 (소유자, 사용자)의 요구를 충족시킬 수 있다. 이런 맥락에서, 대다수 설비 자산의 소유자와 사용자들이 보전 부문에 기대하고 요구한 역할은 돌발적인 고장의 예방과 유효 수명의 연장이 아니라 생산 중단 시간을 최소화하기 위한 신속한 대응이 전부였다. 고장 시점을 예측할 수 없으므로 랜덤하게 발생되는 고장 복원에 필요한 인력을 평준화 할 수 없었다. 최대 부하를 기준으로 인력과 조직을 설계하였고, 예비품 재고 또한 동일하게 적용되었다. 잉여 인력과 예비품은 돌발적 상황의 신속한 복원을 위한 투자였고, 보험이었다.
오늘날, 기업 경영 상황이 급변하였다. 대다수 산업에서 공급이 수요를 상회하기 때문이다. 글로벌 경영 환경은 끊임없는 변화를 요구하고, 경쟁은 심화되고 있다. 원가 경쟁력 향상을 위한 기업의 노력은 대표적인 코스트 센터인 보전 기능에 집중되었다. 보전 기능에 대한 인식과 자원은 투자와 보험에서 필요 악으로 변경되었다. 그 분위기는 가속화되었다.
2000년대 초, ‘Reliability Web’은 그 상황을 조사하였다. 조사 대상 1,000여개 기업의 17%는 OSHA와 EPA 규정에 부합하는 설비 관리가 어려운 수준까지 보전 인력이 감소하였다고 응답했다. 설비 자산의 고장 리스크 예방에 필수적인 인력, 즉 상태 및 예지 보전 의사 결정을 위한 데이터 수집, 분석, 진단 인력을 보유한 조직은 소수에 불과했다. 고장 상황에서 수리, 복원, 교체 인력을 제외한 나머지 조직 기능은 대부분 사라졌다. 즉 미래 동종 고장의 예방에 필요한 작업과 고장 정보 피드백 인력 조차 감소되었다는 것을 의미한다.
덧붙여, 고장 상황의 3R (수리, 교체, 복원) 기능 마저 외주로 대체되기 시작했다. 설상가상, 보전 조직은 보전 전략을 최적화하지 못한 상태에서 지속적인 예비품 재고 감소 요구에 직면하게 되었다. 대량 생산 체계 하에서 소량 다품종 생산으로 변화되고 있지만, 조직의 보전에 대한 요구는 원가 절감이었고, 보전 조직의 보전 전략은 신속한 대응 (파이어 파이팅 보전, 반응 보전)에서 벗어나지 못한 체, 신속한 대응을 가능하게 했던 인력과 예비품 또한 단기 원가 절감을 위하여 희생되었다. 고장 예방 측면의 대다수 기능이 사라진 셈이다. 보전 조직은 겨우 발생된 고장을 복원할 뿐이다.
이 상황에서 설비 자산의 고장 리스크는 점진적으로 증가하였다. 자동화의 영향이다. DCS와 PLC가 보급되었다. 제 3의 산업 혁명이다. 2020년 독일은 제 4의 산업혁명을 주도하고자 국가적 노력을 기울이고 있고, 대한민국은 IT.SW, IOT (사물 인터넷) 등의 융합에 근거한 제조업 혁신 3.0에 이어 스마트팩토리와 디지털 전환 (DT)를 지원하고 있다. 자동화는 사람의 생력 (省力)을 의미하고, 프로세스와 설비의 복잡화를 의미한다. 신뢰성의 감소를 의미하고 고장 발생 결과의 증가를 의미한다 (사람 인변 자동화와 대비되는). 즉 고장 리스크의 증가를 의미한다. 오늘날 물리적 자산의 고장으로 인한 사고가 점진적으로 많아지고 있다.
설비 자산관리 분야의 혁신에 단초가 된 파이퍼 알파 플랫폼 폭발, 그리고 챌린저 호 폭발, 멕시코만 원유 누출 사고 등 설비 자산의 고장 결과를 잘 알고 있다. 설비 고장에 따른 총 손실 규모 또한 증가하고 있다. 홀름베르그에 따르면 핵발전소의 1일 가동 정지에 따른 경제적 영향은 4억 5천만 원, 석유화학 공장은 1억 5천만 원에 달한다.
고장 상황의 신속한 복원과 교체, 수리는 고장결과를 허용하는 전략이다. 소를 잃고 신속하게 마구간을 고쳐 봐야 의미가 없다. 미국과 UK를 중심으로 자산 관리에 대한 인식이 달라지기 시작했다. 증가하고 있는 고장 리스크에 대한 분명한 인식에서 비롯되었다. 하루 강아지는 호랑이를 무서워하지 않는다. 공장과 설비 자산의 신뢰성, 전 생애 수명 관리에 대한 관심이 높아졌다. 설비 자산관리 전략의 수립, 허용되지 않는 리스크를 확정하기 위한 의사결정 체계, 허용되지 않는 리스크의 인식, 그리고 잠재적 고장을 효율적으로 교정하기 위한 작업의 기획과 계획, 안전하고 정밀한 교정 작업 (CM)의 실행과 지속적 개선에 관심을 기울이는 경영진이 등장하기 시작했다. 보전 기능이 설비 자산관리 기능으로 변화되었다. 변화의 실체는 고장 상황에 대한 반응적 대응에서 선행적 대응이다. 반응적 대응의 중대성 인식과 선행적 대응 필요성은 ERP PM 모듈, CMMS (Computerized Maintenance Management System, 설비 자산관리 정보 시스템)/EAM (Enterprise Asset Management) 시스템, 예지 및 상태 보전 시스템 등에 대한 대규모 투자로 나타났다. ERP PM 모듈, CMMS/EAM 시스템은 단순히 조직의 재무와 비용 관리 기능을 보완하는 시스템이 아니다. 물리적 자산의 전 생애 리스크와 비용을 관리하기 위한 시스템이다.
인식 변화는 비용 절감 대상에서 설비 자산의 고장 리스크 (안전, 환경, 품질, 생산, 비용) 인식에 따른 중대 고장 결과를 예방할 수 있는 유일한 기능, 그리고 전 생애 수명과 비용의 최적 관리로서 경영 수익을 기대할 수 있는 기능이라는 것이다. 보전에서 설비 자산관리로의 변화이다. 설비 자산관리 기능은 고장으로 인한 생산 손실과 품질 불량을 예방함으로써 생산성을 극대화할 수 있는 기능, 즉 제 3의 숨겨진 공장의 가능성이다. 중대 설비 자산에 대한 선행적 예방보전 조직, 시스템, 그리고 프로세스의 운영의 소요되는 지출은 단순한 비용이 아니라 안전과 환경, 생산과 품질 측면의 중대 결과 예방으로 투자 수익율을 기대할 수 있는 수익 센터라는 것이다.
산업계의 필요성 인식의 결과로서 수 많은 단편적인 보전 이론과 방법론들이 개발되었다. 데릭 앤더슨은 그와 같은 상황을 “보전 이론의 정글”이라고 평가하였다. 많은 보전 이론과 방법론은 산업계 전문가, 교육 기관, 컨설턴트 간의 혼란과 마찰을 초래케 했다. 실례로 수리학적 체계를 제안한 사람들은 상태 기반 보전 (CBM)의 무분별한 적용을 비판하고 있다. 이들은 고장 예측에 따른 선행적 보전이 품질 고장 데이터의 수집을 방해한다고 생각한다. 이 같은 상황에서 산업계는 어떤 보전 이론이 적절한지에 대한 심각한 혼란에 빠져 있는 게 지금의 현실이다.
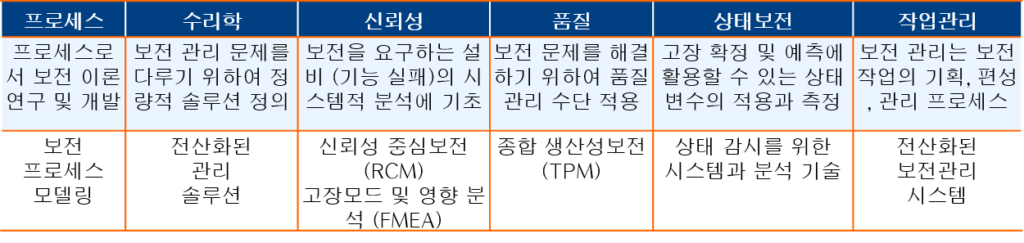
보전 이론 정글은 많은 기업들이 무분별한 유행을 따르는 경우가 많다고 강조한다. CMMS/EAM 시스템이 대표적이다. CMMS/EAM 시스템은 물리적 자산의 전 생애 리스크와 비용을 관리하기 위한 시스템이다. 선행적 예방보전과 계획보전을 운영하는 데 필수적으로 필요한 정보 시스템이다. ‘Reliability Web’의 조사 결과와 동일하게 국내의 경우도 그 본질적인 의도로 활용되는 경우는 소수에 불과할 것이다. 기능의 활용 측면에도 전체 기능의 30% 미만을 활용하고 있다 (IBM 조사 결과).
대다수 방법론은 목표 달성에 일정 부분 기여하지만 기대에 미치지 못했다 (보전 이론의 정글). 2000년대 초, 설비 자산관리 부문에 대한 투자 수익의 극대화, 환경 및 안전 리스크의 최적화 측면에서, 단편적인 방법론이 아닌 전체론적 (포괄적) 접근 방법을 요구하기 시작했다. 2004년, 영국 BSI는 그 요구에 부응하기 위하여 PAS 55를 발표하였다. BSI 산하에서 PAS 55를 문서화한 IAM (The Institute of Asset Management)은 전체론적 관점의 물리적 자산관리 시스템의 적용 결과에 대하여 OPEX의 50%, 계획 운휴 기간의 28 ~ 50% 단축, 안전 사고의 60% 감소, 환경 및 안전 요구의 충족, 그에 따른 기계 및 산재 보험료의 절감 등을 보고하였다. PAS 55는 2014년 1월 최종 ISO 5500X로 전환되었다. ISO 55000 시리즈는 자산 관리를 “조직의 전략적 목표 달성을 목적으로, 자산과 자산 시스템의 전 생애에 걸쳐, 성능과 리스크, 그리고 비용을 최적으로, 지속 가능하도록 관리하기 위한 체계적, 의도적 활동과 노력”이라 정의한다. 많은 관련 전문 기관은 자산 관리에 대하여 다양하게 정의하고 있다. 그 중 하나로서, 설비 자산관리는 “투자에 따른 최대 ROI를 실현하기 위하여, 설비 자산관리 지출로서 최대 성과를 산출하기 위한 설비 자산의 전 생애(자산 취득부터 폐기까지) 관리”이다.
설비 자산관리 활동 (선행적 측면의 강조로서)은 보전 활동 (반응적 활동의 강조로서)과 달리 다음 세가지 활동에 집중하여야 한다.
첫째, 중대한 고장결과를 초래할 수 있는 설비 자산의 돌발적 고장을 제로화하여 조직의 중 장기적 수익성 향상에 기여하여야 한다. 고장 제로는 넌센스다. 그러나 돌발 고장 제로는 실현 가능한 영역이다. 설비 자산관리 활동의 첫 걸음은 자산의 등록 (출생 신고와 같은)에서 출발한다. 등록되지 않는 자산은 선행적으로 관리할 수 없다. 고장의 영향과 결과가 발생할 때, 그 존재를 알 수 있다. 유해 가스 감지기의 기능이 항상 적절하게 유지 (보전)되도록 관리하지 않을 때, 유해 가스가 발생된 상황에서 안전 사고의 발생 가능성을 제로화할 수 없다.
돌발 고장의 제로화는 조직 내 모든 자산을 등록하고, 위험성 (중요도)을 평가한 다음, 중대 결과를 초래할 수 있는 설비 자산에 대하여, 고장원인 제거, 고장모드 감지, 또는 고장결과 예방에 유효한 선행적 예방보전 직무의 선정, 그 다음, 그 직무의 실행 결과로서 산출된다. 다시, 조직은 이를 위한 인력, 프로세스, 시스템에 투자하여야 하고, 설비 자산관리 기능은 중대한 고장결과의 예방으로서 조직의 수익성과 안전성 향상에 기여하여야 한다.
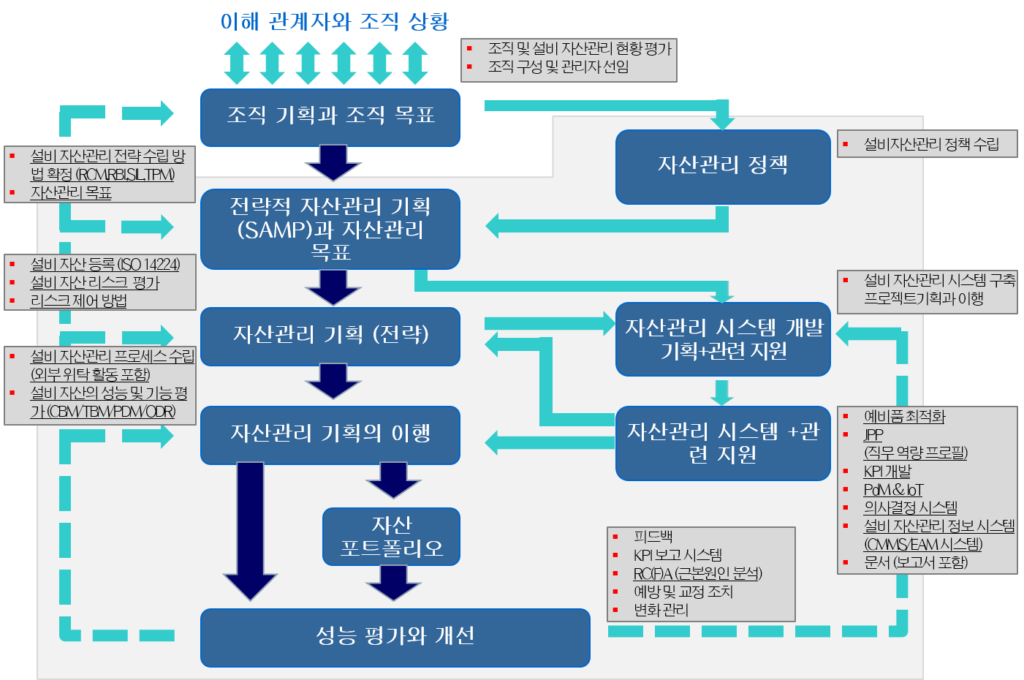
둘째, 유효한 선행적 예방보전 직무로서 감지한 잠재적인 고장을 기능적 고장의 발생 전에 효율적으로 교정함으로써 조직의 생산성에 기여하여야 한다. 돌발 작업은 계획 작업 대비 3 ~ 5 배 (생산 손실을 고려할 경우, 평균 10 배 이상)의 시간과 인력을 요구한다. 돌발적 상황에서 작업 전 위험 예지 훈련은 현실적으로 적용하기 어렵다. 따라서 돌발 작업 중의 안전 사고 발생 가능성은 높아진다. 오늘날 보전 인력의 평균 노동 생산성은 25% 정도, 베스트 프랙티스는 65% 수준으로 알려져 있다. 그 차이는 작업 지연, 그리고 인력과 장비의 대기로부터 발생한다. 조직은 인식한 결함을 계획적으로 교정할 수 있도록 CMMS/EAM 시스템, 작업의 기획 및 계획 프로세스, 그리고 예방보전과 계획보전 인력에 투자하여야 하고, 설비 자산관리 기능은 조직의 작업 효율성, 안전성 향상에 기여하여야 한다.
셋째, 설비 자산의 설계와 개발 단계에서 결정된 유효 수명 전반을 활용할 수 있도록 함으로써 조직의 수익성 향상에 기여하여야 한다. 설비 자산은 개념 및 검토, 설계 및 개발, 제작 또는 설치 국면을 거쳐 운영되다가 폐기되는 라이프 싸이클 (생이 주기)을 가진다. 설비 자산의 유효 (설계) 수명은 시스템적 근본원인, 물리적 근본원인, 인적 근본원인 (해야 할 일을 안 하는 것, 하지 않아야 할 일을 하는 것)으로부터 고장 메커니즘, 그리고 결함을 거쳐 고장, 그리고 고장 결과에 이른다. 설비 자산의 수명은 다양한 요인의 결합으로 단축된다. 그러므로 유효 수명 전반을 활용한다는 것은 고장 근본원인의 제거로서 기대할 수 있는 결과이다. 조직이 단기적 수익에 긍정적인 영향을 미치는 최저 낙찰가를 신뢰하고, 부품과 설비의 설계와 기술적 측면을 간과하는 것, 그리고 고장 예방과 감지를 위한 인력 (또는 조직)을 배치하지 않는 것은 시스템적 근본원인이다. 모든 설비 자산의 고장 리스크는 여기서 시작된다. 조직이 설비 자산의 최적 관리를 위한 조직 구성, 교육 훈련에 투자할 때, 설비 자산관리 기능은 설비 자산관리 전략 수립, 고장 해석과 근본원인 분석에 근거한 설비 자산의 최적 유효 수명으로 조직의 수익성 향상에 기여하여야 한다.
설비 자산관리의 중요성은 점진적으로 증가하고 있다. 생산 및 생산 지원 시스템 에서 설비 자산의 의존도가 증가하고 있기 때문이다. 너무나 많은 조직이 설비 자산관리에 대한 지출을 낭비로 고려하고 있다.
우리가 자동차 타이어의 트레드가 2mm일 때, 타이어를 교체한다면, 잔존 2mm의 트레드는 낭비가 아니라 안전과 고장 결과를 예방하기 위한 투자로 보아야 한다. 생산 설비에 대한 우리 조직의 인식이 어떤지 깊이 고민해 보아야 할 때이다.
